The constant challenge in semiconductor and electronics manufacturing is to increase throughput while also increasing accuracy with shrinking dimensions. This means in-line inspection and metrology systems must provide 100% analysis at a high precision while maintaining high throughput. The latest innovations in ultra high-resolution image sensors and subsequent cameras support these goals. High resolution, high-speed metrology cameras enable greater throughput in semiconductor or electronics inspection and metrology systems through:
- Increased data acquisition time
- Reduced number of scan positions/images per device
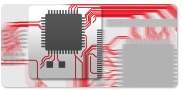
Increased data acquisition time
Higher throughput can be achieved through higher frame rates. With measurements requiring multiple images per sight, as is typical in many 3D methods, the overall speed of the system can be increased with the ability to acquire the images faster. Some OEM cameras also offer Region of Interest (ROI) functionality, which can reduce the image to only necessary information and further increase the frame rate.
One of the challenges with OEM industrial camera design is to ensure no image quality loss when running at full speeds. This means starting with an excellent image sensor. Some of the best in their class are the CMV12000 from CMOSIS and the Vita25k from ON Semi, which offer 12 Megapixels and 25 Megapixels, respectively, and both are high-speed global shutter CMOS image sensors. These sensors are designed to handle these high data rates within a critical timing tolerance to reliably produce quality images. Then within the camera, the image sensor must be driven strategically to provide the best performance and then combined with a reliable interface to ensure no quality is lost. There are several new high-speed interfaces to handle the data rates of the latest image sensors. CoaXPress is one such interface. For example, a 12 Megapixel camera can provide 180 full frames per second over CoaXPress (8-bit data).
Reduced number of scan positions/images per device
To improve the efficiency of inspection systems, the path travelled by the devices/objects to test needs to be planned optimally with minimal movements. A metrology camera with 12 and 25 Megapixels, for instance, provides a larger field of view capturing more of the object per image, reducing the number of scan positions per object.
In order for the full benefits of the larger field of view to be realized, every pixel must be usable which requires uniform, blemish-free images. Uniformity challenges increase as a larger optical field-of- view requires more complex optics and the number of defects pixels in the image sensor increases. Grading the incoming sensor, dedicated processing and blemish elimination in the manufacturing process and camera operation, are some of the things that can be done for high-resolution images with high uniformity.
To continue innovating, semiconductor and electronics process control equipment manufacturers rely on metrology cameras with uniform and stable images at constantly increasing frame rates and resolutions.