In long-range observation and situational awareness systems, the focus lies on observation, surveillance, and reconnaissance. To successfully accomplish these tasks, advanced image systems are needed. Adimec specializes in rugged cameras with high image quality under extreme outdoor conditions. While designing the TMX camera series, Adimec used its extensive application knowledge to aid the design process. This blog will explain the concept of DRI and how it influences camera design.
Observation applications require cameras to detect objects, humans, or animals. A key word in this sentence is detect. But what does it mean to detect something? In the 1950s, a standard was developed to quantify this aspect of observation called DRI (Detection Recognition Identification). At first, the standard applied solely to the use of thermal imaging cameras. Later, this standard was expanded to cameras that use visible and near infrared (NIR) light.
To understand DRI, we first need to dive into the Johnson criteria. The Johnson criteria evaluate the visibility and distinguishability of objects within an image, especially of low-contrast details. They are based on the signal-to-noise ratio (SNR) and provide quantitative thresholds that an imaging system must meet to ensure a certain image quality. The Johnson criteria define the required resolution to ensure a 50% probability of detection, recognition, and identification of an object at a specified distance. This can be done in either the spatial domain or the frequency domain.
Now that we have a basic understanding of DRI, let us focus on why it is important. Consider the following situation: a truck is positioned 1 km away from the Adimec camera (see figure 1).
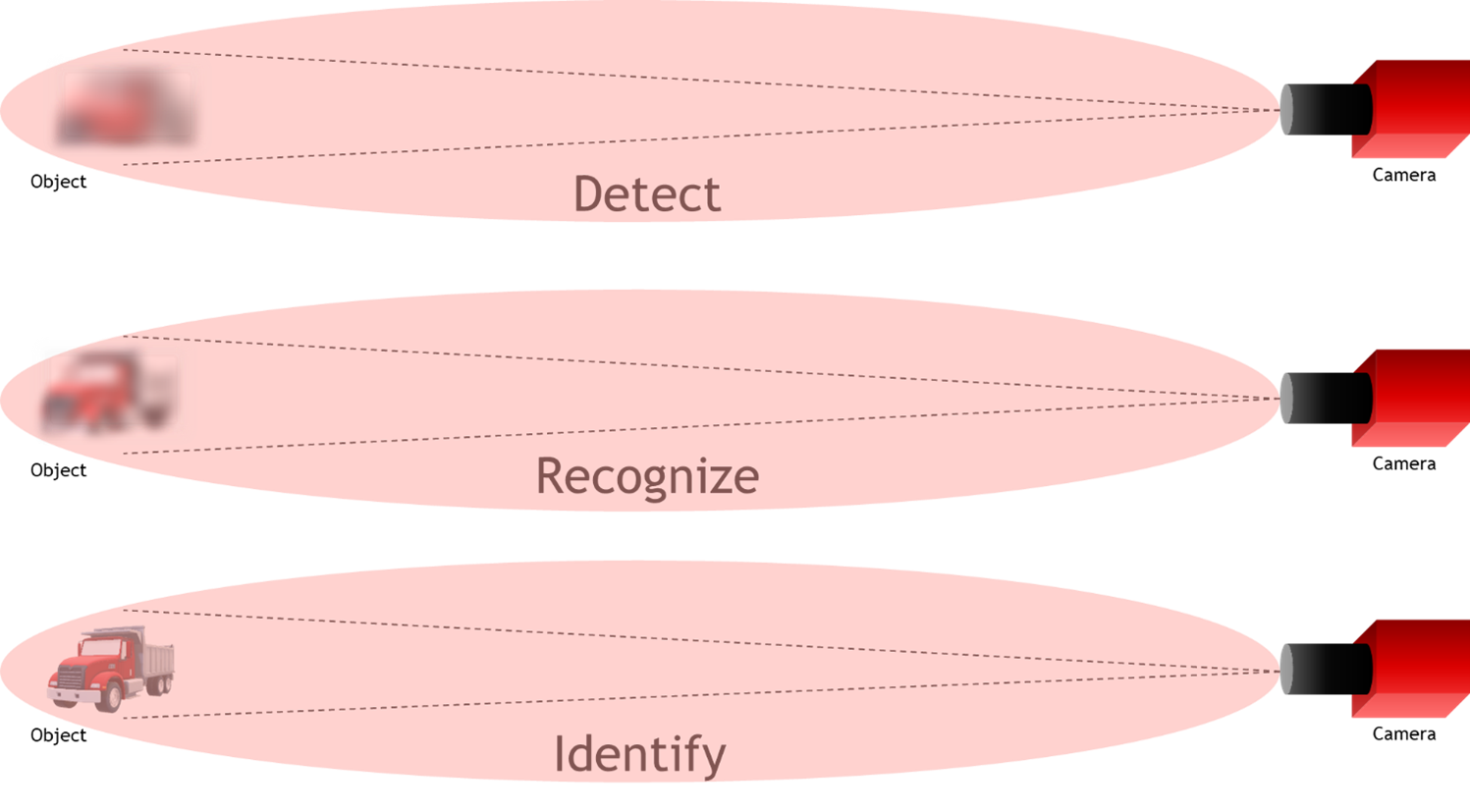
Figure 1 example of a theoretical DRI situation.
The pink oval represents the atmosphere and possible obstacles the light needs to pass through.
The atmosphere and its turbulence can cause additional distortion to the image.
According to the Johnson criteria, 0.9 line pairs per mm (lp/mm) are required to detect the object with sufficient contrast to its surrounding. The camera can then detect that there is an object present in the scene. To confirm that the object is a truck, the criteria define that an MTF of 4.5 lp/mm is needed. Lastly, we want to confirm what kind of truck this is. Identifying the truck requires an MTF of 8.0 lp/mm, according to the criteria. If the camera lens assembly meets these requirements, there is a 50% probability that this object can be detected, recognized, and identified at a distance of 1 km. An example of the line pairs required for DRI of different objects are given in Table 1. These values are based on the Johnson criteria. However, DRI values can be adapted to the intended application of a customer.
Detection | Recognition | Identification | |
[lp/mm] | [[lp/mm]] | [[lp/mm]] | |
Truck | 0.9 | 4.5 | 8.0 |
Human | 1.5 | 4.8 | 8.0 |
Table 1 DRI values for a truck and human
DRI can be an important consideration in selecting a camera for observation applications, and it can guide design choices during Adimec’s development process. Important characteristics during sensor selection include pixel size, resolution, sensitivity, noise behaviour, and quantum efficiency. Several of these characteristics are captured by the MTF of the image sensor, for which we have developed a new measurement system. Depending on the intended application, some of these sensor characteristics matter more than others. In low-light situations, large pixel sizes and low read noise are important for DRI performance. In situations with more light, small pixel sizes and high MTF will give the best DRI performance. The focus of DRI is to maximize resolution and contrast.
In addition to the sensor, the lens also has a large impact on DRI. The lens contributes to both the sensitivity and MTF of the system. Adimec has developed a volume production method to optimize the MTF for large aperture camera lens assemblies.
But also, the Adimec true accurate imaging™ image processing can contribute to the best possible DRI performance of the camera. During the design of the TMX camera line, Adimec created a Video Enhancement Module (VEM) that optimizes the image contrast based on real-time measurements. It eliminates the effects of a hazy atmosphere due to fog and/or sunlight scattering, so that you can see farther. It also optimizes the image contrast in low-light or noisy environments, while keeping the contrast similar across a moving image and changing light levels. With this contrast enhancement feature, the image processing directly improves the DRI performance.
Another interesting type of image processing is Adimec’s proprietary Adaptive ResolutionTM . This feature was developed to fit any new camera to existing optics and interface/displays: for example, when replacing a CCD camera with a CMOS camera that has a smaller pixel size. Advanced interpolation algorithms for cropping and scaling in the camera create virtual pixels of the required size. This results in the same field of view, combined with a better system performance in terms of sensitivity and dynamic range. This in turn leads to better DRI.
The TMX camera series also includes several image-processing features — such as color processing, white balance and image sharpening — that influence the perception of an image. These features do not enhance contrast, but will still indirectly improve the DRI performance. We will write more about this in our next blog.
In conclusion, when selecting a camera, it can be difficult to predict the camera performance based on sensor features such as quantum efficiency or MTF. DRI is an important parameter which describes the camera performance in real-world applications. This practical measure of performance has guided many design choices during the development of the TMX series to optimally suit global security applications.